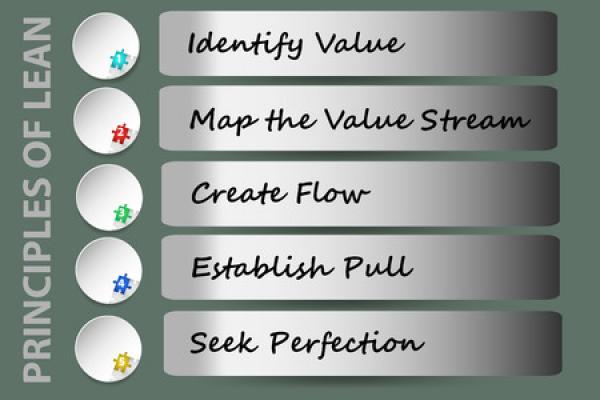
Last month, we covered the origins of lean manufacturing in this space with a promise to discuss the more modern applications this month. As was stated then, lean manufacturing traces its roots back to Japan more than 100 years ago.
In the time since then, it’s evolved in many ways and its principles are now used by businesses all over the world. While the phrase “lean manufacturing” was coined by American businessman John Krafcik in the 1980’s, it was defined for modern times by American researchers James Womack and Daniel Jones in their 1996 book “Lean Thinking.” Here is the process they described:
Define Value
In the most basic sense, the value of a product is determined by what a customer is willing to pay for it. However, it’s not always easy for a company to know exactly what a customer finds valuable. But the business can use techniques such as web analytics, surveys, demographic information and interviews to decipher exactly what a customer wants, how they want it and the price they’re willing to pay for it.
Map the Value Stream
Once you’ve defined the value, the business must identify everything that contributes to the value. Anything that does not add to the value is considered either necessary or unnecessary waste. The first should be reduced as much as possible while the second should be eliminated completely. Doing so allows you to continue to deliver a high-quality product or service while saving both time and money.
Create Flow
The next goal is to ensure that the manufacturing process runs smoothly and doesn’t have too many delays. This may involve reconfiguring steps in the production process to be more efficient, creating a more level workload, training employees to adapt easily and creating cross-functional departments.
Establish Pull
Pull-based systems are another way of eliminating waste and increasing efficiency. Essentially, the goal is to create products when they are needed only in the quantity needed, so that no materials are wasted. By using this system properly, you’ll have exactly the right amount of materials needed to produce a quality product with nothing wasted or left over.
Pursue Perfection
The pursuit of the perfect lean manufacturing system involves following the first four steps and continuing to improve at them as a company every day.
Companies across the world apply these principles to their manufacturing in an effort to deliver the best product to the customer in as efficient a manner as possible. Among those businesses is Fireblast Global. You can learn more about lean manufacturing by touring our facility. Call us at 800-716-1977 to learn more today!