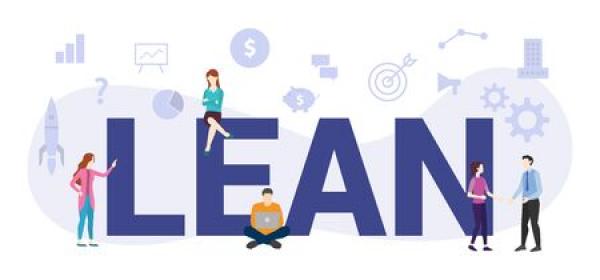
Lean manufacturing is a phrase that’s thrown around a lot in the business world today. It refers to a firm’s method of eliminating waste in all forms in order to deliver the most value possible to the customer.
The term “lean manufacturing” wasn’t actually coined until the late 1980’s by an American businessman. But concept described by the phrase traces its roots back nearly a century and thousands of miles away from the United States.
Today, some version of lean manufacturing is used by plants all over the country and world. But where did it get its start? Here’s a brief history on the origin of the concept:
The Toyota Production System
In the early parts of the 20th century, large-scale assembly manufacturing was still relatively new. Companies were beginning think beyond their previous regional distribution to the national and global level. This created a need for efficient, quick and consistent production.
The biggest breakthrough came in the early 1930s when Toyota’s Taiichi Ohno and Eiji Toyoda developed what was then called “The Toyota Way” but is now known as the Toyota Production System. The aim of the system was to develop the right process to create a sustainable system that creates more value and less waste.
Waste
A key aspect of lean manufacturing was the elimination of waste. Japan was a poor country with a lack of natural resources and a small labor force, so being efficient was key to being competitive. The process defined the eight types of waste as wastes of overproduction, transportation, excess inventory, defects, overprocessing, motion, waiting, and unused employee genius.
Principles
The Toyota Production System uses 14 principles to eliminate all types of waste, while increasing efficiency. These essentially boil down into four ideas, with the first being to focus on a long-term philosophy, even at the expense of your shorter-term financial goals. The second idea is when problems occur to always focus on the process, not the employee, to ensure you get the right results.
Third, it’s important to focus on developing your employees in the long term by investing in them, supporting them and working to improve the environment in which they work. Last, you should drive organizational learning by solving problems and using mistakes as teachable moments for workers at every level.
Eventually, this system spread across the entire world, including the United States, and has evolved greatly since then. Read more about more modern applications of lean manufacturing in this space in three weeks. In the meantime, if you’d like to tour a facility that uses lean manufacturing concepts, Fireblast Global is the place to go. Sharing our process is our way of paying it forward. Give us a call at 800-716-1977 to learn more today!